As a business owner, you're a master of juggling. But amidst the chaos of sales, marketing, and customer service, have you considered what truly makes or breaks your promise to the customer? It's not just your product. It's your warehouse.
In the engine of commerce, the warehouse is the powerhouse. It’s far more than a space to store goods; it’s a dynamic hub dictating the speed, accuracy, and profitability of your entire operation. Effective warehouse management is the art and science of perfecting every process within its walls—from the moment goods arrive to the second they land in the hands of a happy customer.
For small and medium-sized businesses (SMBs), mastering this is not an operational choice—it's a critical factor for survival and growth. This guide is your blueprint for that mastery. We will dissect the warehouse cycle, expose the costly errors hiding in plain sight, and illuminate the path from manual chaos to automated control.
Why Warehouse Management is Your SMB's Secret Weapon
For SMBs with tight margins, the warehouse's performance reverberates through every financial report. Poor management bleeds cash and erodes customer trust. Excellent management directly fuels your growth.
- Financial Impact: An efficient warehouse minimizes the holding costs of excess inventory—storage fees, insurance, and the risk of obsolescence. By optimizing stock, you free up vital cash that would otherwise be trapped on a shelf, directly improving the cash flow essential for an SMB’s survival.
- Sales Impact: You can't sell what you can't find. An organized warehouse is your best defense against stockouts, which send customers straight to your competitors. Real-time inventory visibility empowers your sales team to sell with confidence.
- Customer Service Impact: In today's market, speed and accuracy are not perks; they are expectations. Showing an item in stock online only to cancel the order because it's lost in the warehouse creates a "lousy customer experience" that inflicts lasting brand damage.
"Many small business owners see their warehouse as an expense to be minimized. The shift in mindset happens when they see it as the heart of customer satisfaction. A well-run warehouse doesn't just save money; it actively earns loyal customers."
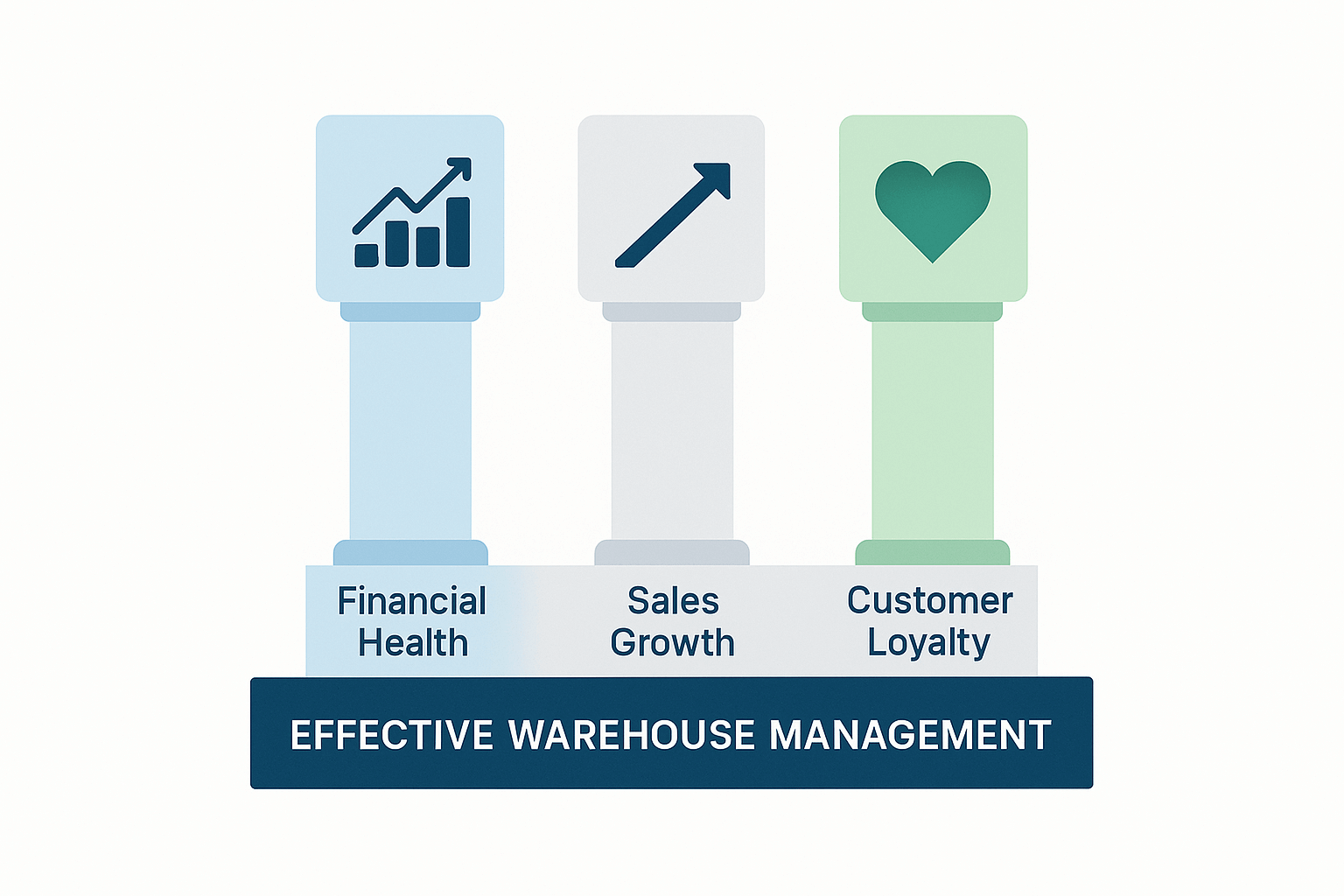
The A-to-Z Warehouse Cycle: A Process Masterclass
To optimize your warehouse, you must first master its operational rhythm. Each stage is a link in a chain; a weakness in one compromises the entire system.
1. Receipt of Goods: Your First Line of Defense
This is the most critical control point. An error here—a miscount, a failure to note damage—poisons your data from the start.
Process:
- Verification: Meticulously check incoming shipments against the Purchase Order (PO) to confirm items and quantities.
- Quality Control: Inspect all goods for damage. This is your only chance to file a claim with the supplier.
- Tagging & Logging: Immediately tag items with barcodes or SKUs and log them into your inventory system. The stock update must be instantaneous.
The Power of Documents:
The key documents are the Purchase Order (PO), the supplier's Packing Slip, and your internal Goods Received Note (GRN). These enable the three-way match—a cornerstone of financial control where you compare the PO, GRN, and the final supplier invoice to ensure you only pay for what you ordered and correctly received.
2. Storage and Putaway: A Place for Everything
Once received, goods must be stored for easy access and optimal space use in a process called putaway. Haphazard placement is a recipe for lost time and lost inventory.
The Foundation: Address-Based Storage
The modern warehouse is mapped like a city. The space is divided into unique locations (e.g., Aisle 01, Rack 04, Shelf B, Bin 03), and each item is assigned to a specific "address". This eliminates searching. Advanced warehouse management systems are built on this very principle, providing the granular location data needed to make finding items effortless.
Smart Placement Strategy (ABC Analysis)
Store your fastest-moving, highest-value products (A-items) in the most accessible locations (e.g., near the shipping area) to drastically reduce travel time for your team.
3. Order Picking: The Labor Battleground
Picking is often the most labor-intensive and costly operation in the warehouse. Its efficiency is paramount. The accuracy of the picklist, which is generated by your inventory system, is everything. An error on the picklist guarantees an incorrect shipment, leading to costly returns and unhappy customers.
4. Shipment: The Final Handshake
This is the last checkpoint before an order reaches your customer, and your last chance to get it right. The process includes packing, correct labeling, final verification, and dispatching with the carrier, ensuring your system updates the stock levels automatically.
The Silent Killers: Common Errors and Their Real-World Cost
Imagine this: it's your busiest season. An order comes in for your best-selling product. Your system says you have 20, but the shelf is empty. Your team scrambles, searching frantically while another order for the same item arrives. The customer waits. Sound familiar? This isn't a rare catastrophe; it's the daily reality for businesses bogged down by small, compounding warehouse errors.
Error Type | What It Looks Like | The Brutal Consequences |
---|---|---|
Spreadsheet Reliance | Using manual data entry in Excel for inventory tracking. | Financial: Cost of fixing constant errors. Efficiency: Immense time sink, not scalable. Customer: Delays due to outdated info. |
Haphazard Storage | No defined location for items; "put it wherever there's space". | Financial: Sky-high labor costs for searching/picking. Efficiency: Wasted hours locating items, slower fulfillment. |
Inventory Discrepancy | Your records show 50 units, but you physically have 45 (shortage) or 55 (overage). | Financial: Lost sales from stockouts; tied-up capital and holding costs from overages. |
Ignoring Your Data | Not tracking inventory turnover, picking speed, or error rates. | Financial: Poor purchasing decisions, missed profit opportunities. Customer: Persistent stock issues due to bad forecasting. |
"The most dangerous phrase in a growing business is 'it's just a small error.' In a warehouse, small errors compound daily. They are the silent killers of profit margins and customer loyalty."
The Path to Optimization: Process and Technology
How do you break this detrimental cycle? The solution is a two-pronged attack: standardize your processes, then accelerate them with technology.
Step 1: Standardize Everything
Before software can help, you need clear, documented workflows for every task. A core component is implementing regular inventory counts (stocktaking) to maintain accuracy.
Stocktake Type | Description | When to Use It |
---|---|---|
Full Physical Inventory | Counting every item in the warehouse at once. Highly disruptive. | Annually for financial reporting. |
Cycle Counting | Counting small, specific sections of inventory on a rotating schedule (e.g., A-items weekly). | Continuously, to maintain accuracy with minimal disruption. |
Step 2: Embrace Smart Automation
Automation is the accelerator that eliminates the manual, error-prone tasks holding you back. For an SMB, this doesn't mean expensive robots. It means:
- Barcode & RFID Scanners: The single best tool to eliminate data entry errors and boost speed.
- Centralized Inventory Management Software (IMS): The brain of the modern warehouse.
Choosing Your Weapon: A Guide to Warehouse Software
Trying to run a modern warehouse on spreadsheets is like navigating a metropolis with a hand-drawn map. It's time for a GPS. Here are your options:
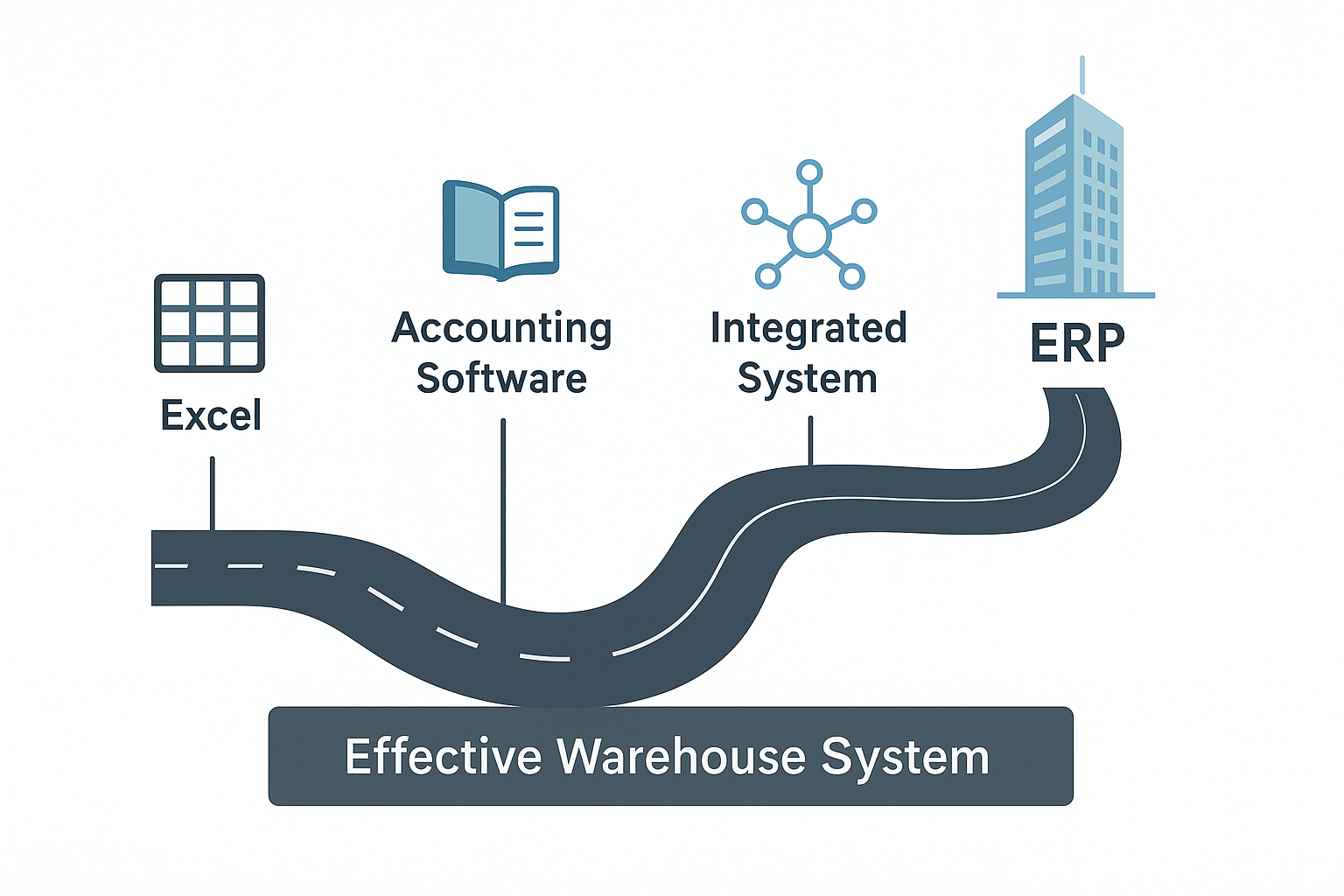
Software Type | Human-Friendly Description | Best For... |
---|---|---|
Excel/Spreadsheets | The Digital Notebook. It's familiar, but every entry is manual, and every mistake is yours to find. | Startups with very few products. Quickly outgrown. |
Simple Accounting Software | The Financial Guardian. Tracks that you sold an item but has no idea where it was or how it was picked. | Businesses where finance is the main need, with very simple fulfillment. |
Integrated Systems | The Central Nervous System. Connects your warehouse to your entire business. A sale automatically triggers a picklist and updates stock levels in real-time. A single source of truth. | Most growing SMBs seeking to eliminate data silos and have sales, inventory, and finance perfectly synchronized. |
ERP Systems | The Corporate Skyscraper. Integrates every business function (HR, manufacturing, CRM). Immensely powerful, but often too complex and expensive for many SMBs. | Larger, complex businesses, often in manufacturing or multi-site distribution. |
Frequently Asked Questions (FAQ)
What is the most critical first step to improve my warehouse?
Establish 100% accurate inventory tracking. Start with a meticulous receiving process and maintain it with relentless cycle counting. Without knowing exactly what you have and where it is, all other efforts are compromised.
What is the difference between warehouse management and inventory management?
Inventory management is the strategic "what and when" (what to order, when to order it). Warehouse management is the physical "where and how" (where it's stored, how to move it efficiently). A great integrated system manages both seamlessly.
How do I choose between FIFO and Weighted Average Cost for my inventory?
- FIFO (First-In, First-Out) is ideal for businesses with perishable goods or products with a shelf life (like food or electronics) as it aligns with the natural physical flow.
- Weighted Average Cost is simpler for businesses with homogenous, high-volume products where tracking individual purchase costs is difficult (e.g., hardware, components).
How much automation do I really need?
For 99% of SMBs, the journey starts and succeeds with two things: barcode scanning and a centralized inventory management system. This combination solves the most significant sources of error and inefficiency. You can explore the full range of options in our detailed article about warehouse management software.
Conclusion: Your Foundation for the Future
Effective warehouse management is no longer a luxury for large corporations; it's an essential, accessible discipline for any SMB that wants to compete and win.
By standardizing your processes, committing to accuracy, and leveraging smart, integrated technology, you transform your warehouse from a liability into your most powerful asset. You stop letting manual errors and lost inventory dictate your potential. You take control. You delight your customers. You build a more profitable, scalable, and resilient business. This journey can seem daunting, but every step towards clarity is a step towards a stronger future.